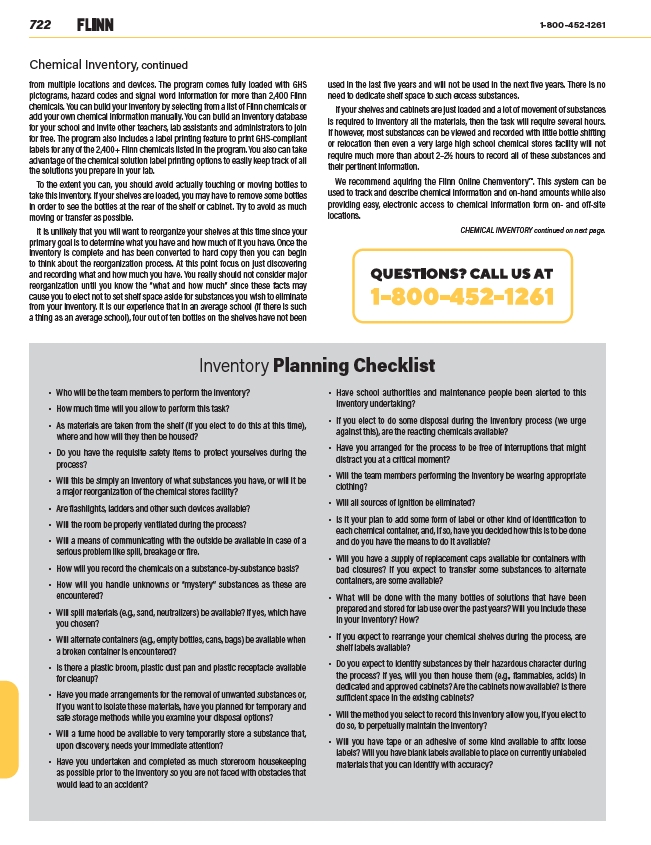
722 1-800-452-1261
Chemical Inventory, continued
CHEMICAL INVENTORY continued on next page.
Inventory Planning Checklist
• Who will be the team members to perform the inventory?
• How much time will you allow to perform this task?
• As materials are taken from the shelf (if you elect to do this at this time),
where and how will they then be housed?
• Do you have the requisite safety items to protect yourselves during the
process?
• Will this be simply an inventory of what substances you have, or will it be
a major reorganization of the chemical stores facility?
• Are flashlights, ladders and other such devices available?
• Will the room be properly ventilated during the process?
• Will a means of communicating with the outside be available in case of a
serious problem like spill, breakage or fire.
• How will you record the chemicals on a substance-by-substance basis?
• How will you handle unknowns or “mystery” substances as these are
encountered?
• Will spill materials (e.g., sand, neutralizers) be available? If yes, which have
you chosen?
• Will alternate containers (e.g., empty bottles, cans, bags) be available when
a broken container is encountered?
• Is there a plastic broom, plastic dust pan and plastic receptacle available
for cleanup?
• Have you made arrangements for the removal of unwanted substances or,
if you want to isolate these materials, have you planned for temporary and
safe storage methods while you examine your disposal options?
• Will a fume hood be available to very temporarily store a substance that,
upon discovery, needs your immediate attention?
• Have you undertaken and completed as much storeroom housekeeping
as possible prior to the inventory so you are not faced with obstacles that
would lead to an accident?
• Have school authorities and maintenance people been alerted to this
inventory undertaking?
• If you elect to do some disposal during the inventory process (we urge
against this), are the reacting chemicals available?
• Have you arranged for the process to be free of interruptions that might
distract you at a critical moment?
• Will the team members performing the inventory be wearing appropriate
clothing?
• Will all sources of ignition be eliminated?
• Is it your plan to add some form of label or other kind of identification to
each chemical container, and, if so, have you decided how this is to be done
and do you have the means to do it available?
• Will you have a supply of replacement caps available for containers with
bad closures? If you expect to transfer some substances to alternate
containers, are some available?
• What will be done with the many bottles of solutions that have been
prepared and stored for lab use over the past years? Will you include these
in your inventory? How?
• If you expect to rearrange your chemical shelves during the process, are
shelf labels available?
• Do you expect to identify substances by their hazardous character during
the process? If yes, will you then house them (e.g., flammables, acids) in
dedicated and approved cabinets? Are the cabinets now available? Is there
sufficient space in the existing cabinets?
• Will the method you select to record this inventory allow you, if you elect to
do so, to perpetually maintain the inventory?
• Will you have tape or an adhesive of some kind available to affix loose
labels? Will you have blank labels available to place on currently unlabeled
materials that you can identify with accuracy?
from multiple locations and devices. The program comes fully loaded with GHS
pictograms, hazard codes and signal word information for more than 2,400 Flinn
chemicals. You can build your inventory by selecting from a list of Flinn chemicals or
add your own chemical information manually. You can build an inventory database
for your school and invite other teachers, lab assistants and administrators to join
for free. The program also includes a label printing feature to print GHS-compliant
labels for any of the 2,400+ Flinn chemicals listed in the program. You also can take
advantage of the chemical solution label printing options to easily keep track of all
the solutions you prepare in your lab.
To the extent you can, you should avoid actually touching or moving bottles to
take this inventory. If your shelves are loaded, you may have to remove some bottles
in order to see the bottles at the rear of the shelf or cabinet. Try to avoid as much
moving or transfer as possible.
It is unlikely that you will want to reorganize your shelves at this time since your
primary goal is to determine what you have and how much of it you have. Once the
inventory is complete and has been converted to hard copy then you can begin
to think about the reorganization process. At this point focus on just discovering
and recording what and how much you have. You really should not consider major
reorganization until you know the “what and how much” since these facts may
cause you to elect not to set shelf space aside for substances you wish to eliminate
from your inventory. It is our experience that in an average school (if there is such
a thing as an average school), four out of ten bottles on the shelves have not been
used in the last five years and will not be used in the next five years. There is no
need to dedicate shelf space to such excess substances.
If your shelves and cabinets are just loaded and a lot of movement of substances
is required to inventory all the materials, then the task will require several hours.
If however, most substances can be viewed and recorded with little bottle shifting
or relocation then even a very large high school chemical stores facility will not
require much more than about 2–21⁄2 hours to record all of these substances and
their pertinent information.
We recommend aquiring the Flinn Online Chemventory™. This system can be
used to track and describe chemical information and on-hand amounts while also
providing easy, electronic access to chemical information form on- and off-site
locations.